Molds
About our molds
- Injection: Cold, hybrid and hot casting. Screw-off system, mechanical and hydraulic skids.
Products: Ideal for producing plastic parts with complex shapes, such as electronic components, product housings, toys, automobiles, etc. - Materials: Different types of plastics can be used, including thermoplastic plastics such as polypropylene, polyethylene, ABS, and others.
- Precision: The process offers high precision and repeatability in the production of parts.
Maintenance: Injection molds can be complex and expensive, but they allow for efficient series production. - Blow molding: Extrusion, blow and injection, thermoformed blow molding.
Products: Mainly used to produce containers such as bottles, jars, drums, and other hollow plastic products. Blow molding is also suitable for the manufacture of large parts with internal cavities. - Materials: The process generally uses thermoplastic plastics such as PET (polyethylene terephthalate), polyethylene (PE), and polypropylene (PP).
- Cost and time: Blow molds are generally simpler and faster to manufacture than injection molds, and products are also produced more quickly.
- Part design: Blow molded parts generally have a hollow structure and can be lighter than injection molded parts.
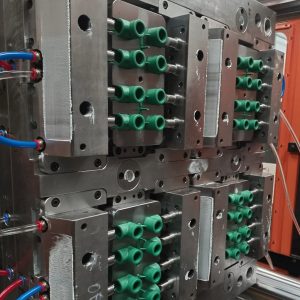
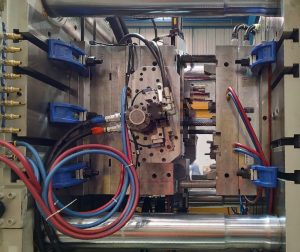
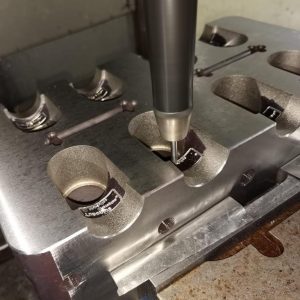
Previous
Next
Electro erosion
Electrical discharge machining is a machining process that uses controlled electrical discharges to remove material from a workpiece. This process is primarily used to work hard metals or materials that are difficult to machine using conventional methods, such as milling or turning.
- The process is carried out in a bath of dielectric liquid (such as oil or water), which insulates the electrode and workpiece parts while facilitating the removal of material fragments.
- A series of electrical discharges occur between the electrode and the workpiece. Each discharge generates a small spark that melts and evaporates the workpiece material at that point.
- The discharges are high intensity, but short duration, allowing precise control of material removal.
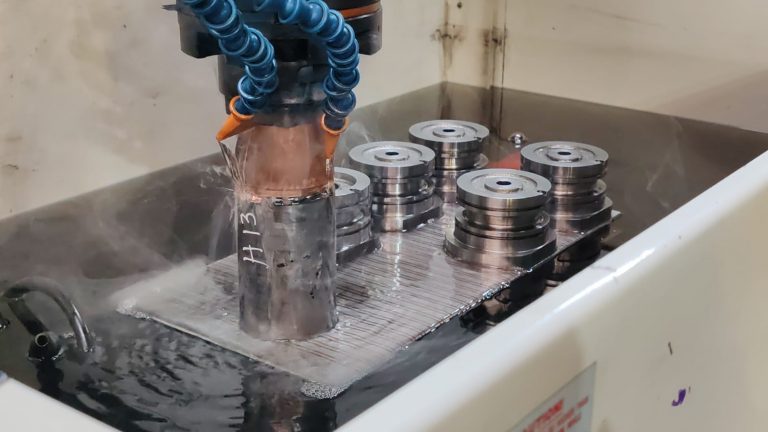
Hot Casting Systems
Unlike cold runner systems, these systems have a direct impact on reducing or eliminating resin waste. By also reducing overall cycle times, energy consumption is lower and there is a higher volume of parts produced per molding cycle even when using multi-cavity molds.
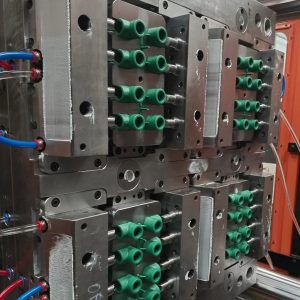
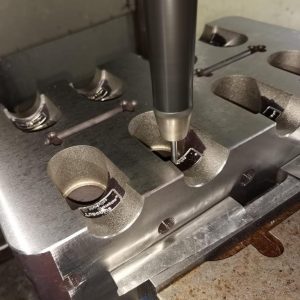
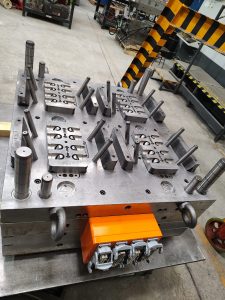
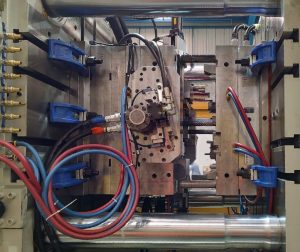
Previous
Next
Contact
Telephone
01 (722) 2169364.
ventas@polisol.com.mx